TM 1-1500-204-23-8
(a)
Wash and scrub weld in hot running water
until all traces of flux have been removed.
(b)
Immerse part for one minute in
chromepickle solution with the following composition:
Sodium dichromate ..................................... 1 1/2pounds
Nitric acid..................................................... 1 1/2 points
Water....................................................to make 1 gallon
Wash in cold running water.
(c)
Boil welded part for 2 hours in a solution
of 8 ounces of sodium dichromatic in 1 gallon of water.
Rinse in cold water, followed by dipping in boiling water.
Air dry the part.
(8)
Inspection. Examine weld for cracks,
porosity, excessive flux inclusion, and similar defects.
c. Magnesium Arc Welding. Arc welding may be used
for all type joints commonly used on steel. This type weld
is approximately five percent stronger than other type
welds. The following paragraphs describe magnesium arc
welding practices and procedures.
(1)
Joint preparation. Prepare joints using
the following procedures:
(a)
Sheets from 0.125 to 0.250 inch thick
should be scarfed or beveled.
(b)
Sheets more than 0.250 inch thick should
be scarfed on both sides.
(2)
Gas. Use argon, MIL-A-18455, or helium,
for shrouding the arc.
(3)
Electrodes. Tungsten, ranging in size
from 3/32 to 1/2 inch, should be used. Electrode should
not extend any farther from gas shielding cup than
necessary, about 1/4 to 3/8 inch.
(4)
Machine settings. Suggested settings for
good operation are given in table 3-5. Currents shown
are for all alloys except magnesium, Federal Specification
QQ-M-44, which requires 5 to 10 amperes more current
for stock up to 0.050 inch and 15 to 30 amperes more
current for thicker material. Sheets thicker than 0.150
inch should be welded in more than one pass, using 60
amperes on first pass and current shown in table 3-5 for
subsequent passes. Argon requires 1/3 to 1/2 flow of
helium.
(5)
Arc welding procedures.
Arc weld
magnesium using the following procedures:
(a)
Strike arc on magnesium surface.
(b)
When metal becomes molten under arc,
advance filler rod arc. Do not push arc into puddle.
(c)
Move torch and rod along at a constant
speed.
(d)
Flow of inert gas should be continued for
several seconds after extinguishing arc to prevent
excessive oxidation.
(e)
When welding sections differ greatly in
thickness, heavier sections should be preheated with a
gas torch to 350° F (177° C).
(6)
Defect repairs.
Repairs for defects
encountered while arc welding magnesium are explained
in the following paragraphs.
(a)
Cracking. When cracking is encountered,
starting and stopping plates may be clamped at each end
of seam. Weld is started in one plate and continued
along joint to other plate in one continuous operation.
(b)
Warpage. Warpage may be overcome by
heating to a temperature not exceeding 500° F (260° C)
and then pressing or hammering with a wood or leather
mallet.
(c)
Stress relief.
In case of stressed
functional parts, stress relief is accomplished by securing
assembly in a suitable jig and heating, as shown in table
3-6. After heating, cool in air free from drafts.
(7)
Post cleaning. Clean weld with a wire
brush.
(8)
Inspection. Examine weld for porosity,
inclusions, cracks, undercutting, overcutting, overlapping,
and similar defects.
d.
Spot Welding. Spot welding should be used in
low stress applications such as secondary or noncritical
aircraft structures. The following paragraphs describe
magnesium spot welding practices and procedures.
3-14
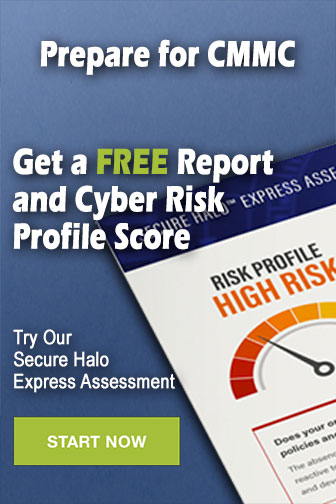