TM 1-1500-204-23-8
3-18 Change 1
(4)
Arc welding procedures. The following pro-
cedures will produce welds of good quality:
(a)
Grind tungsten electrode to an approxi-
mate 60-degree point (included angle).
(b)
Do not attempt to strike an arc in a mol-
ten (weld) pool.
(c)
Regrind electrode if arc is accidentally
struck in molten pool.
(d)
Use gas welding flux, MIL-F-7516, as
applicable, sparingly on underside of weld area when
necessary to control oxidation.
(e)
Use only gas welding rods as applica-
ble or as specified in paragraph (a).
NOTE
Maximum length of electrode protruding from
gas cup should not exceed 1/4 inch.
(f)
Adhere closely to amperage, voltage,
gas flow and electrode size as specified in table 3-8.
(5)
Inert-arc welding. A comparatively recent
development in arc welding, which is referred to as inet-
arc, has earned wide recognition in the field of corrsion-
resistant steel and nickel alloy welding, particularly as
applied to thin sheet, 0.050-inch thickness and under.
The use of this process in fabrication of thin sections
produces welds having very good strength and ductility.
This type of welding was originally applied to magne-
sium, with helium gas as the shielding medium. Although
helium may also be used in welding of steels and nickel
alloy in heavier sections, argon gas is preferred on thin
sections due to difficulties encountered in establishing
the arc with low current setting when using helium. A
lower arc voltage is required to establish and maintain
the arc with use of argon. The arc in argon envelope has
the appearance of a gas welding flame, whereas helium
produces a blunt or ball-like flame. Direct current with
straight polarity is used in welding steels and nickel alloys
by this process. The arc welder used with this special
equipment should conform to MIL-W-80019.
e. Corrosion-Resistant Steel Spot Welding. Spot
welding may be used on low carbon steels, austenitic
steels, hardenable steels, and nickel alloys. The follow-
ing paragraphs describe spot welding practices and pro-
cedures.
WARNING
Drycleaning solvent is flammable, and sol-
vent vapors are toxic. Use P-D-680, Type II
Solvent in a well-ventilated area. Keep away
from open flames. Avoid prolonged solvent
contact with skin.
(1)
Cleaning. Clean surfaces to be welded of
objectionable films, such as oxides, scales, ink, grease,
or dust, using a clean rag or bristle brush moistened with
drycleaning solvent, Federal Specification P-D-680.
(2)
Spot spacing. The edge distance will be so
that no deformation or bulge will occur at edge of sheet.
(3)
Surface indentation. Where aerodynamic
consideration is a requisite, the electrode indentation
shall not exceed 0.003 inch. In all other cases, indenta-
tion is not acceptable when depth exceeds 10 percent of
sheet thickness.
(4)
Defects. Weld defects such as voids, blow
holes, porosity, and cracks shall not exceed the following
limits:
15 percent of area of the weld nugget in the
plane in which the measurement is taken, or a
linear dimension greater than 25 percent of the
weld diameter.
No internal defect shall extend to within 15 per-
cent of weld diameter of the boundaries of the
case weld structure.
(a) Welding Stresses and Distortion. In
welding of corrosion-resistant steels or nickel chromium
iron alloy, care must be taken to avoid welding stresses
and distortion as much as possible. In making joints,
sheets should be spread slightly apart and tack welded.
The amount of spread will depend on whether arc or gas
welding is employed, less spread being required with
arc than with gas welding. For this reason, and the fact
that there is less tendency toward carbide precipitation
in welding of corrosion-resistant steels with use of the
former, the arc process is recommended.
The arc
process is particularly recommended on applications
where it is impossible to allow for expansion
and
contraction of material. The distribution of contraction
stresses can be further improved by using back step
welding in which electrode is advance a short distance
ahead of weld and joint is welded back toward original
starting point.This process is repeated until weld is
completed. When practicable, jigs shall be used to hold
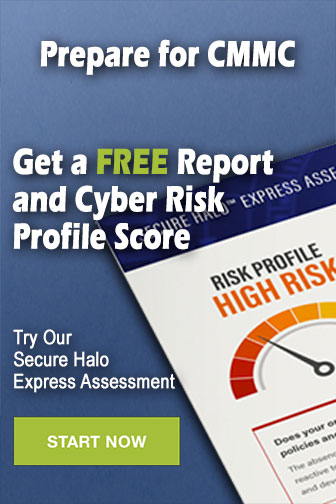