TM 1-1500-204-23-8
3-16 Change 1
WARNING
Hydrochloric acid is highly toxic and corro-
sive. Goggles, rubber gloves, and rubber
aprons should be worn when handling the
acid and the acid solution. Do not inhale
gases and mists. When spilled on the body or
clothing, wash immediately with large quanti-
ties of cold water, and seek medical help. Do
not pour water into acid when preparing the
solution; instead, pour acid into water. Always
mix acid and water slowly. Perform operations
only in well-ventilated areas. Otherwise,
death or injury may result.
(1)
Make a test solution by dissolving 10 grams
of cupric sulfate, Federal Specification O-C-828, in 100
cc of hydrochloric acid, Federal Specification O-C-275.
(2)
With a medicine dropper, place one drop of
solution on sample to be tested and allow it to remain in
contact with metal for two minutes.
(3)
At the end of two minutes, slowly add, one
drop at a time, three to four drops of water to solution on
metal. The copper will not be deposited on metal until
water is added.
(4)
Wash and dry sample.
NOTE
If sample is corrosion-resistant steel, the acid
cupric sulfate solution will be deposited on
metal leaving a copper colored spot. If sample
is a nickel-base alloy, a white spot will be left
at point where solution came into contact with
the metal.
This test will distinguish only the class of
material; however, as a general rule, only sta-
bilized corrosion-resistant steel, AMS 5512,
and occasionally nickel chromium iron alloy
are used in exhaust stacks and collector
rings. Due to various conditions, and several
types of corrosion-resistant steels used in
structural parts and higher chrome nickel cor-
rosion-resistant steel used in turbosuperchar-
gers, this test can be used as a guide only. A
hardness test may also assist in determining
condition.
b. Special Welding Considerations. Corrosion-re-
sistant (stainless) steels and nickel chromium iron alloy
(Inconel) present certain problems in fabrication that are
not encountered in more commonly used low carbon and
low alloy steels. The 18-8 stabilized corrosion- and heat-
resistant steels and nickel chromium iron alloy are quite
frequently used for very similar applications. However,
there is a great difference in composition and a lesser
degree of difference in working of these two materials.
(1)
Nickel chromium iron alloy. The nickel chro-
mium iron alloy contains approximately 75 percent
nickel, 15 percent chromium, 9 percent iron, and 1 per-
cent manganese, and is classed as a nickel-base alloy.
(2)
Corrosion-resistant steels. 18-8 steels con-
tain approximately 18 percent chromium, 8 percent
nickel, and balance iron with small amounts of other ele-
ments varying with the particular type of 18-8, and are
classed as steels. Welding of any of the corrosion-resist-
ant steels in work-hardened condition shall be accom-
plished only in specific application as directed in applica-
ble technical manuals.
NOTE
Of the 18-8 series of corrosion-resistant
steels, only those types with maximum car-
bon content of 0.08 percent and unstabilized
(type 304) or maximum carbon content of
0.10 and stabilized with titanium or colum-
bium (types 321 and 347 respectively) AMS
5512, corrosion- and heat-resistant, and in
annealed condition, have excellent welding
qualities. Types 316 and 317, corrosion-resis-
tant steels, although classed with 18-8 series,
have higher percentages of nickel, or both
nickel and chromium, plus from 2.00 to 4.00
percent molybdenum. These two types are
not suitable for welding with the electrodes or
gas rods carried under MIL-R-5632. A special
electrode, identified as KA2SMO, is provided
for welding these types. The balance of this
series has only fair to poor weldability.
c. Corrosion-Resistant Steel Gas Welding. The fol-
lowing paragraphs describe gas welding practices and
procedures.
(1)
Rod selection. The welding of 18-8 corro-
sion-resistant steels and nickel chromium iron
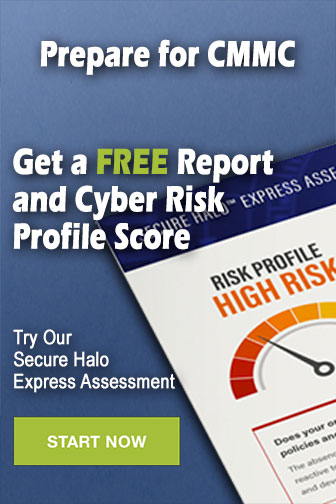