TM 1-1500-204-23-8
3-12 Change 1
(c)
Welds should be made in one pass
whenever possible.
(3)
Striking the arc. The following procedures
are for striking the electric arc when arc welding alumi-
num.
(a)
Brush electrode over surface of base
metal like striking a match, as shown in figure 3-5.
Attempts to strike an arc by touching electrode to the
piece to be welded will usually cause sticking.
NOTE
A short arc (1/8 to 3/16 inch) is most
desirable.
(b)
When arc goes out, restart arc 1/2-inch
back of preceding crater to avoid burning through sheet.
e. Aluminum Spot Welding. The following para-
graphs describe aluminum spot welding practices and
procedures. Confine spot welding to alloys 1100 and
3003, and Alclads 2219, 5052, 5083, 5086, 5454, 5456
and 7075.
(1)
Preparation. Position equipment and con-
trols to prevent current flow until force is applied to the
electrodes.
Figure 3-5. Brush Method of Starting
Electric Arc.
(2)
Spot spacing. Spacing will not exceed 1/8
inch between welds in the same row and 1/16 inch
between welds in adjacent rows.
(3)
Joint thickness. Joint thickness must not
exceed four times the thickness of the thinner material.
NOTE
Do not join more than two sections of the
material by one spot weld.
(4)
Machine settings. Machine settings are
given in the applicable maintenance manual.
(5)
Weld sequence. Start all welds at center of
sheet and work toward each end.
3-6. Magnesium Welding. Welding of magnesium
can be accomplished by the use of gas, arc, or spot weld,
depending on the alloy, nature of the parts, and the end
usage. The following paragraphs cover cleaning proce-
dures and procedures for gas, arc, and spot welding.
WARNING
The vapors from some chlorinated solvents
(e.g., carbon tetrachloride , trichloroethylene,
and perchloroethylene) break down under the
ultraviolet radiation of an electric arc to form
a toxic gas. Avoid welding where such vapors
are present. Furthermore, these solvents
vaporize easily and prolonged inhalation of
the vapor can be hazardous. These organic
vapors should be removed from the work area
before welding is begun.
a. Cleaning. Clean oil , grease, and dirt from area to
be welded using acetone or denatured alcohol[. After
cleaning, remove oxide or chemical treatment using steel
wool. Sand, mill, or file abutting edges to give a clean,
smooth surface and to remove edges left by shearing.
b. Magnesium Gas Welding. Oxyacetylene, oxyhy-
drogen, or oxycarbohydrogen gas may be used for this
method of welding. Oxycarbohydrogen is the preferred
gas. Limit gas welding to butt or corner joints because the
flux is an active corroding agent and must not become
entrapped in the weld. The following paragraphs
describe magnesium gas welding practices and proce-
dures.
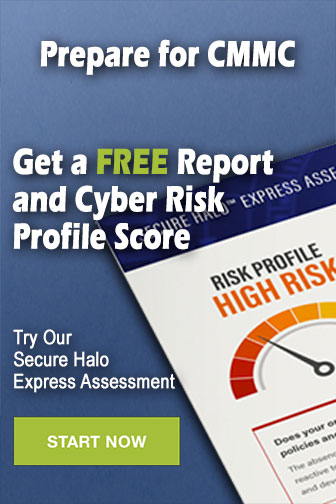