TM 1-1500-204-23-8
Change 1 3-13
(1)
Joint preparation. Prepare joints using the
following procedures:
(a)
Stock less than 0.040-inch thick may be
flanged 1/16 to 1/8 inch.
(b)
Sheets 0.040- to 0.125-inch thick are
simply butted together leaving 1/16- inch gap.
(c)
Sheets thicker than 0.125 inch should
be beveled to a 90-degree vee, leaving 1/16-inch root-
face.
(2)
Flame adjustment. Use a neutral flame.
Gas pressure and orifice diameter vary with thickness of
material (refer to table 3-4).
(3)
Jigs. Secure all work in jigs.
CAUTION
In case of a magnesium fire, use clean, dry
sand or talcum powder, Federal Specification
A-A-42, or clean, dry, unrusted cast iron
chips. Sprinkle a 1/2-inch layer over area. Do
not use water or any standard liquid or foam-
type fire extinguisher: an explosion may
result.
(4)
Tack weld. After brushing on flux, tack weld
at intervals of 1-1/2 to 3 inches.
(5)
Finish weld. Finish weld using the following
procedures:
(a)
Preheat workpiece using a fanning
action with the torch. This procedure gradually fuses the
flux .
(b)
Hold rod in outer flame until base metal
starts to melt, forming a puddle.
(c)
Move torch along in a straight line as
rapidly as possible.
(d)
Dip rod into puddle intermittently.
(e)
Lift torch slowly at end of welded seam
to avoid rapid cooling.
NOTE
When any part of weld starts to burn, welding
should be stopped and burned area scraped,
cleaned, and refluxed before resuming.
(6)
Buckling. If buckling or warping of seam
welds in flat sheets occurs, use the following procedures:
(a)
Straighten minor warping by hammer-
ing with a wood or leather mallet.
(b)
Large distortions must be preheated to
600 to 700°F (316 to 370°C) before hammering.
(7)
Post cleaning.
As soon as work has
become cool enough to handle, clean using the following
procedures:
Table 3-4. Guide to Regulation of Gas Welding Equipment
Metal
thickness
(inches)
Rod
diameter
(inches)
Oxygen
pressure
(psi)
Orifice
diameter
(inches)
Pressure
(psi)
Orifice
diameter
(inches)
Pressure
(psi)
0.020
1/16-3/32
14
0.035
13
0.040
14
0.032
1/16-3/32
35
0.035
13
0.046
35
0.040
3/32-1/8
35
0.035
13
0.059
35
0.051
3/32-1/8
35
0.035
13
0.059
35
0.064
3/32-1/8
35
0.040
35
0.059
35
0.072
3/32-1/8
35
0.040
35
0.059
35
0.081
3/32-1/8
35
0.046
35
0.059
35
0.091
1/8-5/32
35
0.046
35
0.067
35
0.128
1/8-5/32
35
0.059
35
0.081
35
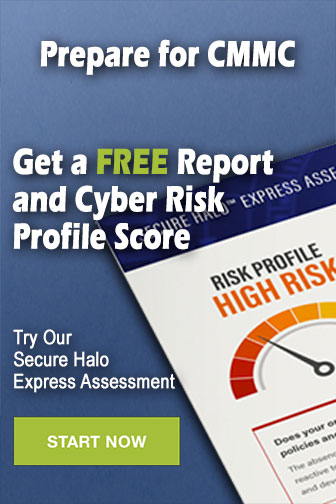