TM 1-1500-204-23-8
Figure 3-4. Gas Welding Flames
(3)
Jigs. Use jigs designed to minimize heat
loss using point contact. All contact points should be
rounded, including holddown clamps, to permit aluminum
to expand while materials are being welded. It is also
desirable to tack weld whenever possible.
(4)
Flame adjustment. The welding flame, as
shown in figure 3-4, should be neutral in order to achieve
the best speed and a clean weld of good soundness.
(5)
Welding technique. Gas weld using the
following
procedures:
(a)
Apply flux to welding rod and surface to
be welded.
(b)
Pass flame over starting point in small
circles until flux melts.
(c)
Scrape rod over surface at about 3- to 4-
second intervals, permitting rod to come clear of flame
each time, otherwise rod will melt before parent metal and
it will be hard to note when welding should start.
(d)
After flux melts, base metal must be
melted before rod is applied.
NOTE
The forehand method of welding is best
for aluminum because the flame points
away
from
the
complete
weld
and
preheats the edges to be welded.
(e)
Remove flux residue by scrubbing with a
bristle brush and hot water; immerse part in a 10 percent
solution of sulfuric acid, Federal Specification O-S-809,
rinse, and dry with compressed air.
(f)
Visually examine completed weld for
cracks, porosity, fusing defects, and undercutting. Chip
and grind out damaged welds before rewelding.
NOTE
Never use a torch to remove a weld.
d.
Aluminum Arc Welding. Arc welding should be
accomplished using inert gas to shield the arc. The use
of inert gas as a shield produces a clean, sound weld
without the use of corrosive fluxes. Defects, probable
causes, and remedies are given in table 3-3.
(1)
Gas. Use either argon or helium for the
shield. Argon, MIL-A-18455, is the preferred gas.
(2)
Electrodes. Electrodes used for arc
welding should conform to AWS A5.10. Use electrodes
according to the following procedures:
(a)
Hold electrode in a nearly vertical
position.
(b)
Move electrode along seam in a straight
line at a uniform rate.
3-9
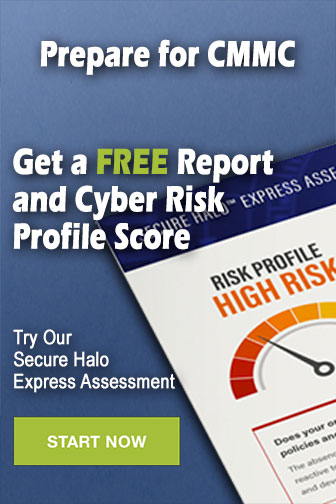