TM 1-1500-204-23-8
alloy by gas welding process shall be accomplished using
the following rods:
Corrosion-resistant steel - steel welding rod, MIL-
R-5632, Type II, Grade 3G.
Nickel chromium iron alloy - nickel chromium iron
alloy welding rod, AWS A5.9.
(2)
Flux. The welding flux to be used in gas
welding of these metals is MIL-F-7516. The flux shall be
mixed in accordance with instructions on container, or
technical
grade
methanol
(wood
alcohol),
Federal
Specification O-M-232, can be mixed with corrosion-
resistant flux to form a thin paste. Water will be mixed
with nickel chromium iron alloy flux to also form a thin
paste. The undersurfaces of joint will be liberally coated
with paste and light coating applied to rod. Paste will be
used sparingly on top surfaces only when under- surfaces
are inaccessible. Under no circumstances shall it be used
excessively on top surfaces.
(3)
Tip selection. The welding tip should be
one or two sizes smaller than those used in welding of low
carbon steels of the same thickness.
(4)
Flame adjustment. The welding flame
should be slightly reducing with an excess acetylene
feather not exceeding 1/16 inch. (See figure 3-4.) In other
words, flame should be as near neutral as possible
without the possibility of having either an oxidizing or
carburizing flame, both of which are detrimental to
ductility of metal. A soft flame should be used since a
harsh flame, although adjusted to appearance of being
neutral, is actually oxidizing.
(5)
Exhaust welding. When making up a
section of an exhaust manifold or similar part, a short
flange, 1/32 to 1/16 inch in length, can be formed to the
edge or edges and may be left straight to make a butt
weld. The joint is then covered with a thin coating of flux
and tack welded every two or three inches. On very thin
material, it may even be necessary to tack weld at closer
intervals. If buckling is encountered during tacking
operation, part shall be reshaped before proceeding with
welding operation. Prior to welding operation, seam shall
be refluxed in accordance with instructions contained in
paragraph (2).
NOTE
The procedures outlined in paragraphs (1)
through (5) are to be followed in both
tacking and welding seams. Under no
circumstances will corrosion-resistant steel
or nickel chromium iron alloy aircraft parts
be welded by gas process without use of
flux of proper grade.
d. Corrosion-Resistant Steel Arc Welding. The
following paragraphs describe arc welding practices and
procedures.
(1)
Electrode selection. The welding of 18-8
corrosion-resistant steels, and nickel chromium iron alloy,
by the metallic arc welding process, will be accomplished
using the following electrodes:
Corrosion-resistant steel- electrode, corrosion-
resistant steel, MIL-R-5632, Type I, Grade 3E.
Nickel chromium iron alloy-nickel chromium iron
alloy welding, AWS A5.9, rod (electrode).
(2)
Arc
length.
To
obtain
maximum
efficiency of flux in protecting the molten metal, short arc,
approximately the same length or shorter than diameter of
electrode being used, is a definite requirement. These
electrodes have a heavy coating of flux which helps to
prevent oxidation of the weld metal in its passage through
the arc. Satisfactory welds cannot be made with a long
arc.
(3)
Polarity. Corrosion-resistant and nickel
chromium iron alloy electrodes are generally used with
straight polarity on very thin material to prevent burn
through. Due to many variables in welding machines, arc
characteristics, inaccuracy of voltmeters and ammeters,
differences in individual welder ability, and type of weld
joint, exact welding currents will not be recommended.
For successful corrosion-resistant steel and nickel
chromium iron alloy welding, the best rule to follow is to
use least possible current consistent with proper fusion.
The values established in table 3-7 should be used only
as a guide in adjusting welding current.
3-17
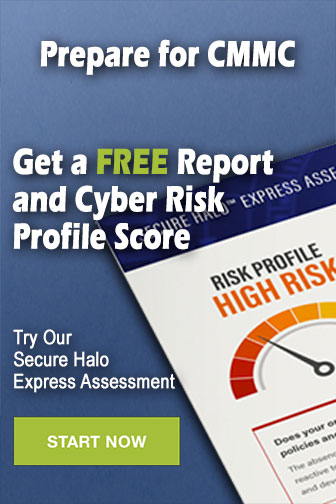