TM 1-1500-204-23-8
Figure 3-3. Welding Equipment Schematic
c.
Fluxes. Fluxes are used to clean and promote
the fusion process when welding. Different fluxes are
used 'or various types of metal. Mix fluxes in accord-
ance with instructions on container.
3-5. Aluminum Welding. The following paragraphs
cover types of aluminum alloys which can be welded,
cleaning procedures, and procedures for gas, arc, and
spot welding.
a.
Types of Alloys Aluminum alloys 1100, 2219,
3003, 5052, 5083, 5086, 5454, 5456, and 6061 may be
welded by the use of gas, arc, or spot weld.
b.
Cleaning. Parts to be welded should be cleaned
and deoxidized using the following procedures:
(1)
Immerse part in solution of 4 to 6 ounces
of alkaline cleaner, MIL-C-87936, per gallon of water,
maintained at a temperature of 180 to 200F (82 to
930C), for 5 minutes.
(2)
Rinse part in cold water.
(3)
Immerse for 1 minute in a solution of 15
to 17 ounces of aluminum deoxidizer (Aldox) or
equivalent, per gallon of water.
(4)
Rinse in water heated to temperature of
170 to 190F (77 to 88C), and air-dry.
(5)
Measure contact surface resistance with a
micrometer. Contact surface resistance must be less
than 1000 microhms.
(6)
Deoxidize parts by one of the following
methods when the inert-arc process is to be used.
(a)
The chemical method consists of
immersing the part in a solution of 10 percent nitric acid,
Federal
Specification
O-N-350,
and
0.25
percent
hydrofluoric acid, MIL-A-24641, for 5 minutes. Rinse in
hot water and dry with compressed air.
(b)
The mechanical method consists
of abrading the edges to be welded 1-1/2 inches deep on
both sides.
c. Aluminum
Gas
Welding.
The
following
paragraphs describe aluminum gas welding practices and
procedures.
(1)
Material thickness requirement. Gas
welding should be confined to materials from 0.031 to
0.125 inch in thickness.
(2)
Edge preparation. On thin material up to
about 1/16 inch thick, edges should be formed to a 90-
degree flange about the same height as the thickness of
the material or higher.
3-5
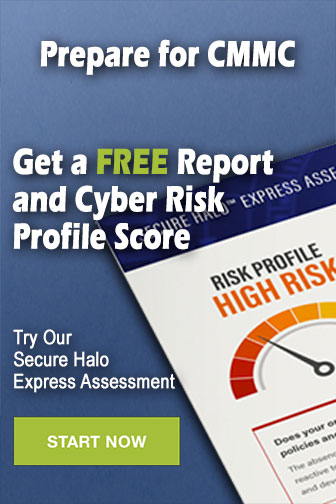