TM 1-1500-204-23-8
(1) Electric arc welding precautions. Observe the
following precautions:
Curtains or screens to prevent flash injury to eyes
shall be provided around arc welding locations where
shop personnel are working.
When connecting ground cable, make sure that the
welding current path will not pass through moving
parts including bearings, gears, or anything which
could be damaged by electric current.
Circuits on electric arc welding machines shall be
examined only when circuits are dead.
Do not operate polarity and rotary switches while
welding equipment is under load.
Provide an adequate power ground to motor
generator and other electrical welding apparatus.
Major repairs to electrical equipment shall be performed
by qualified electricians only.
(2) Electric arc welding equipment. Typical electric
arc equipment is shown in figure 3-2.
(3) Inspection and maintenance. All equipment shall
be inspected periodically. Cables shall be examined for
defects and loose connections and defective electrode
holders shall be replaced. Examine welding terminals for
burning or pitting. Tighten all loose connections and
replace damaged cables. Refer to the applicable
operation and service instructions manual for specific
maintenance of particular type equipment.
c.
Spot Welding. Spot welding is a resistance
welding process that fuses metal together using the heat
obtained from the resistance to the electric current flow
passing through the workpieces.
(1) Spot welding equipment. A schematic of spot
welding equipment is shown in figure 3-3.
(2) Inspection and maintenance. All equipment
shall be inspected periodically. Repair damaged
equipment in accordance with the applicable maintenance
manual.
Figure 3-2. Electric Arc Welding Equipment
3-4. Welding Materials. Electrodes, welding rods, and
fluxes are described in the following paragraphs.
a.
Electrodes. Metal-arc electrodes may be grouped
and
classified
as
bare
electrodes,
thinly
coated
electrodes, and shielded arc or heavy coated electrodes.
The type used depends on the specific properties required
in the weld deposited, such as: corrosion resistance,
ductility, high tensile strength, etc.; the type of base metal
to be welded; the position of the weld (i.e., flat, horizontal,
vertical, or overhead); and the type of current and polarity
required. Steel, aluminum, and magnesium electrodes
are described in table 3-1.
b.
Welding; Rods. Welding rods are made for
various types of carbon steel, cast iron, aluminum,
bronze, stainless steel and other metals, and for hard
surfacing. Welding rods for the different types of welding
are given in table 3-2.
3-4
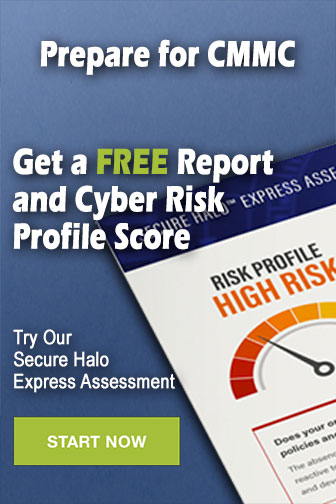