TM 1-1500-204-23-8
(3) Inspection and maintenance. Refer to the applicable
manuals for inspection and maintenance of grinders. The
following paragraphs contain general wheel installation
and dressing procedures.
(a) Wheel installation.
The following procedures
are for installing a new grinding wheel on a grinder (see
figure 2-8):
CAUTION
Do not use a metallic object for testing
soundness of grinding wheel. The wheel may
shatter.
1
Test
wheel
for
soundness
before
installation by holding wheel and tapping it with a piece of
wood. A sound wheel will emit a dull ring.
2
Place blotting between wheel and wheel
flanges. Wheel flanges should be of ample size.
3
Place wheel on arbor and tighten spindle
nut so flanges hold wheel securely.
NOTE
Do not overtighten spindle nut because cracking
of grinding wheel may result.
4
Test grinding wheel for breakage, after
installing, by permitting grinder to run for a few minutes.
(b) Wheel dressing. Use of grinding wheel will
cause the wheel to wear unevenly and not run true.
Grinding wheels shall be dressed as follows in order for
them to run true:
1
Place wheel dresser against wheel and
move back and forth while grinder is running until wheel is
trued.
2
When using wheel dresser, hold dresser
against grinding wheel firmly enough to prevent sparks.
2-5. Laying Out and Mounting Work. General layout
practices and mounting of work pieces are explained in
the following paragraphs.
a. General Layout Practices. Work to be
machined is laid out to establish reference lines or planes
which are used to set up the part on the machine, to
outline the surfaces to be machined, and to show the
approximate amount of metal to be removed from each
surface. The part is painted with a blue layout dye and
layout marks are scribed for reference.
b. Mounting. Mount work piece in machine in the
manner described in the machine operator's manual. Be
sure part is mounted securely to avoid slipping while
machining operation is in progress.
2-6. Special Operations On Drilling Machines.
Special operations on drilling machines include tapping,
reaming, counterboring and spot facing, lapping, and
bearing roll staking.
a. Tapping. Tapping is the process of cutting inside
threads in drilled holes. Provision for rapidly reversing
the spindle must be made so that the tap can be backed
out of the hole after the thread is cut to the required
depth. Refer to the applicable operator's manual for
tapping procedures.
b. Reaming. Reaming is done to finish drilled holes
to an exact diameter with round, straight, and smooth
surfaces. The reamer must be sharp and correctly
ground. Refer to the applicable operator's manual for
reaming procedures.
Figure 2-8. Grinder Wheel Installation
2-10
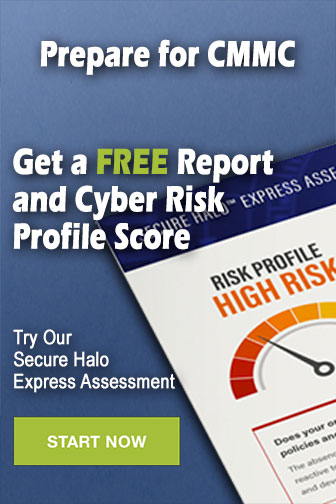